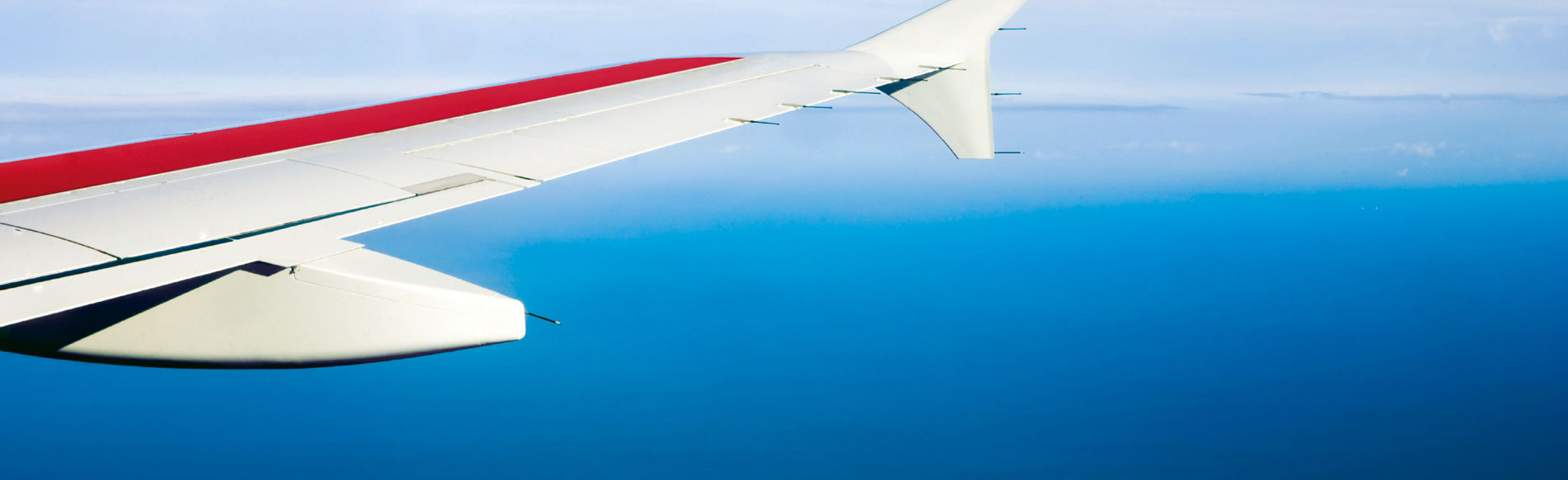
Flight Test Instrumentation (FTI)
Simplicity and Maximum Flexibility in Recording and Analyzing Aircraft Parameters
In aviation, flight test instrumentation is crucial for gathering essential measurement data and parameters required for certification by aviation authorities. Diverse technologies and tools decode and interpret data during flight trials, offering a detailed overview of an aircraft's performance.
Key components include the flight recorder, analog sensor data, switching states, field bus info, and communication protocols like ARINC 429, ARINC 664, or MIL-STD-1553B from the flight control system. The flight control system manages maneuverability and stability, with flight test instruments capture data on control surface configurations, response times, and flight dynamics. Engineers use these measurements to optimize performance and safety.
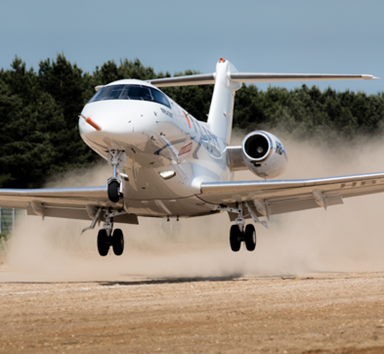
An aircraft manufacturer's ‘Flight Test Instrumentation’ division uses data acquisition systems (DAS or DAQ for short) whose task is to record analogue sensor data. Such systems record several hundred to a thousand measurement channels, the most common sensors being strain gauges and sensors for measuring temperature or vibration. Force, pressure, displacement, angle and flow sensors are also used. In addition to recording the analogue signals, the digital data of the avionics system must also be recorded synchronously. To do this, digital interfaces such as ARINC or MIL-Bus must be able to be read and decoded by the DAQ system.
Aerospace ground equipment acts as an intermediary, enabling real-time communication, data stream monitoring, and seamless information exchange between the aircraft and ground operations. This facilitates reviewing and replicating flight maneuvers, enhancing test process flexibility and adaptability.
Measurement data can be stored within the flight test measurement system or on the flight test engineer's workstation, or transmitted directly to a ground station via IRIG 106 telemetry standards. Aerospace ground equipment includes a reception antenna for telemetry signals, a system for PCM data stream decoding, and the capability to route distinct measurement data to separate workstations. This integration enhances communication and monitoring, streamlining the flight testing process.
Test Stand and Rig Solutions
Customized with a high degree of adaptation
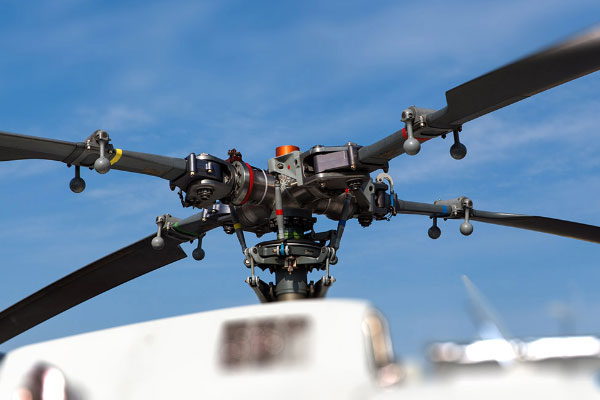
Structural analysis of components (e.g., airframes, wings, rotor blades, landing gear, actuators, motors). Strain and stress measurement and control for calibration, static, fatigue and endurance test beds. Strain measurements on composite materials Turbine engine test cell instrumentation. Integrated automated test stand control and alarm systems.
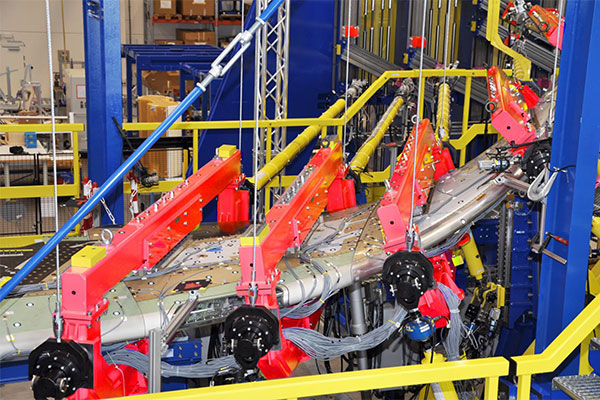
Hardware-in-the-Loop (HiL) solutions for nose-wheel steering, iron bird and ISTR rigs. Development testing of cargo loading systems. Integrated ATP test stands for production and quality control. Development test bed for high-lift systems. Pressure and temperature scanner interfaces for turbine engine test cells. Vibration monitoring hardware and software.
Teidän hyötynne - meidän tavoitteemme
- Myymme kokonaisia ratkaisuja, emme pelkkiä tuotteita
- One-stop shop tehokkaille mittausratkaisuille - kattaen koko testausketjun
- Analogiatulot suodatettuja
- Hajautettu mittauslaite - tehokas, joustava ja luotettava
- TEDS-toiminnallisuus anturien asetuksille
- Yhdenaikainen monikanavainen näytteenotto
- Mittaustulokset nopeasti ja luotettavasti yhdistetyillä laite- ja ohjelmistoratkaisuilla
- Ohjelmoitavat laiteasetukset
- Kattava valikoima kenttäväyliä (mm. ARINC-429, ASCB-D, CAN, RS422)
- Mahdollisuus omiin laajennuksiin